The Importance of Process Simulation in Chemical Engineering
With the ability to accurately model complex systems and processes, process simulation has become an indispensable tool for chemical engineers by providing invaluable insights that lead to better designs, improved safety, and increased efficiency. In this article, we'll explore the critical benefits simulation brings to chemical engineering and why it should indeed be a core part of every chemical engineer's toolkit.
The Cost Savings Are Substantial
The most significant benefits of process simulation are cost savings in capital expenditures and operating expenses by allowing engineers to thoroughly test process designs and operating parameters without the need to build pilot plants, thus preventing expensive design flaws from making it to the construction phase.
This simulation also reduces operating expenses by allowing virtual experimentation to identify energy savings and the optimal configurations for equipment and control systems. In addition, models can be rapidly modified to test different operating parameters rather than having to experiment on a live production line.
Research shows that companies implementing digital manufacturing solutions involving this type of simulation have experienced significant returns on investment, leading most chemical companies to view simulation as a valuable tool to keep production running smoother and boosting profitability. For example, process simulation can help determine optimal operating conditions for a distillation column leading to energy savings and reduced operating costs.
Significantly Improved Safety
Of course, ensuring safety is the top priority for any chemical production facility, which is greatly enhanced by process simulation. By allowing engineers to extensively test process designs for potential safety hazards or undesirable behavior before they are built, safety risks can be eliminated proactively rather than reacting to incidents after the fact.
Modeling hazardous scenarios such as equipment failures, uncontrolled reactions, and unexpected startup/shutdown transients proves useful to Engineers as they can assess potential outcomes and modify the design to include additional instrumentation, controllers, relief systems, containment barriers, and other safeguards accordingly.
This also plays a crucial role in investigating the causes of safety incidents and implementing corrective actions by replicating conditions preceding an incident and identifying a root cause to be determined to apply appropriate measures definitively.
In a study backed by NIOSH and conducted at the University of Iowa's College of Public Health, experts explored how computer-based simulations can enhance employee wellness by creating safer work environments. This approach, called digital human modeling allows forecasting of behaviors and potential hazards and assessing workplace design without endangering workers and incurring the expenses of physical prototypes.
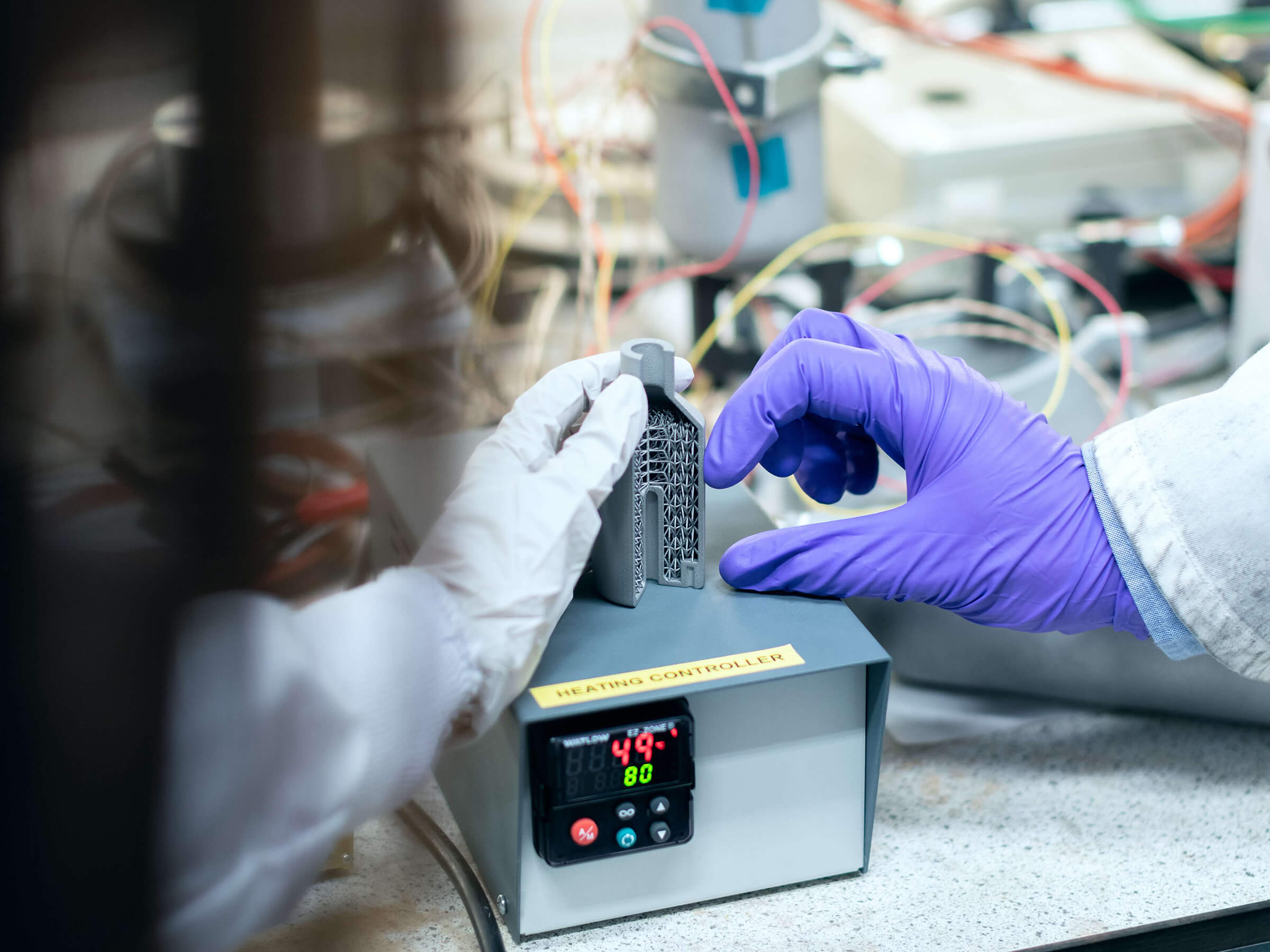
Virtual Commissioning Cuts Costs and Risks
Commissioning new facilities is one of the most costly and challenging undertakings as complex chemical plants become more extensive and intricate making successfully starting a new plant only more complex.
Process simulation revolutionizes this commissioning by enabling virtual factories to be tested and debugged before anything moves forward. This is also known as "digital twinning" when unit operations and control systems are thoroughly tested against the full range of dynamic conditions the actual plant would experience. By doing this, accurate commissioning proceeds faster, smoother, and safer by virtually ironing out any pesky bugs or integration issues.
A good example of this would be BASF, which utilized simulated environments to reduce commissioning time at a plant in Germany by using virtual plant testing with simulation models before startup to minimize costly on-site field testing and modifications allowing the plant to ramp up rapidly. Also, Linde Engineering which has a history of using advanced tools and methods to optimize the construction process has also employed virtual commissioning to reduce the commissioning schedule.
Optimizing Operations
Process simulation applications extend well beyond design and construction and into ongoing plant operation, resulting in many companies using simulation models of their as-built facilities as living digital twins continually updated to reflect changes over time.
The digital twin provides a platform for in-depth operational analysis and optimization allowing Engineers to rapidly evaluate options for improving energy efficiency, increasing throughput, adjusting maintenance schedules, and modifying control strategies.
This type of simulation also powers sophisticated process control systems for running plants at peak efficiency and allows controllers to continuously optimize setpoints and manipulate variables in real-time guided by dynamic simulations parallel to the live process. This model-predictive approach also handles complex interactions between process units that are difficult to manage with traditional single-loop controllers.
Accelerating Innovation
For chemical companies to stay competitive, they must continually seek process innovations that can create value, and process simulation provides an agile digital platform for rapidly researching and testing process technology innovations.
With simulation, Engineers can quickly assess new chemistries, catalysts, equipment concepts, and flowsheet configurations by simulating their performance, allowing the most promising options for further physical prototyping and piloting to be identified and avoiding spending time and money to scale up designs with little potential.
The simulation also provides insight into the dynamics of innovating processing methods and operational requirements, allowing commercialization risks to be understood early so new technologies can be engineered to fit within operational constraints.
For example, ExxonMobil extensively utilized simulation to design and commercialize their new LC-Finer fluid catalytic cracking technology by modeling the thermodynamics, reaction kinetics, and unit operations digitally first, allowing the process to be optimized, thus accelerating deployment.
The Path Forward
Of course, process simulation has demonstrated immense value across the chemical industry from enhancing designs to improving operations, and as simulation tools become increasingly sophisticated and easier to use, adoption will only accelerate.
To leverage this simulation fully, companies should consider the following steps:
- Make simulation an integral part of the workflow for any new facility design project
- Build and maintain digital twin models of existing facilities to support optimization
- Provide simulation capabilities directly to plant operators and engineers
- Apply simulation across the product lifecycle from early-stage R&D to commercialization
- Develop in-house simulation expertise across engineering and operations teams
Mastery of process simulation will be vital for staying ahead in the chemical industry and companies that utilize this technology will undoubtedly reap the benefits of top-level safety, faster scale-up, lower costs, and optimized production all while providing a significant competitive edge that will grow over time as capabilities advance. As we see it, the future of chemical engineering is certainly digital.